When it comes to the health and safety of your staff, you can never be too careful. You will probably have plenty of policies and procedures, but if they aren’t being adhered to in the strictest of ways, then they’re not going to help anyone. When it comes to thinking about your staff, here are a couple tips that can help you ensure you won’t be held liable should an accident happen.
Get a SOP
A SOP is a standard operating procedure. This document will address the correct use of personal protective gear, specialist equipment like hazmat packaging, safe handling, and safe use, and the proper disposal of chemicals. This document can be tailored to cover all of your materials. Use posters, flip charts and handbooks to ensure that you have provided all of your staff with the SOP and a gentle reminder about the hazards of each of the chemicals.
Bear in mind that if you’re handling a lot of chemicals, during things like training and inspections, if you were to have a separate write up for each chemical that would take a lot of time to learn and is open to many more mistakes and confusion – increasing the chance of mishandling.
Housekeeping
It goes without saying that a small spillage on the floor could lead to a significant accident. Keeping your floors clean and dry, free from debris and trip hazards will lower the likelihood that your staff will have a trip or fall.
Within easy reach of all work, surfaces should be super absorbent mat pads so that any chemical spills can be handled quickly. A few bins that are labeled to accept chemical wastes should also be easily accessible.
Work surfaces should be maintained very well too. If the workspace is cluttered, sticky or messy in any way, there is a much higher chance that a spill will occur. Workers need plenty of space to carry out their duties.
Hang signs next to all sinks and drains that no chemicals should be disposed of via that receptacle.
Keep you storeroom in a neat and tidy order. Make sure everything is labeled up correctly too. Put a single person in front of managing stock levels so that reordering will be easier to keep track of also.
Fresh Air
It is imperative that all of your staff have access to decent air flow. Chemical labs and areas can quickly become hot and irritating to the lungs. Although the work will still need to be carried out it is better to minimize exposure as much as possible. Something to be mindful of is having at least 8 to 10 air changeouts per hour when there is staff in the space.
Safety Equipment
Having the correct signs and labels will make a big difference in the everyday management of chemicals and hazardous materials. These will be a constant reminder to staff for how they should handle the disposal procedures. There should also be an eyewash station, which is clean and ready for use at any time, as well as showers, a fire extinguisher, and multiple first aid kits – as well as someone on each shift with training.
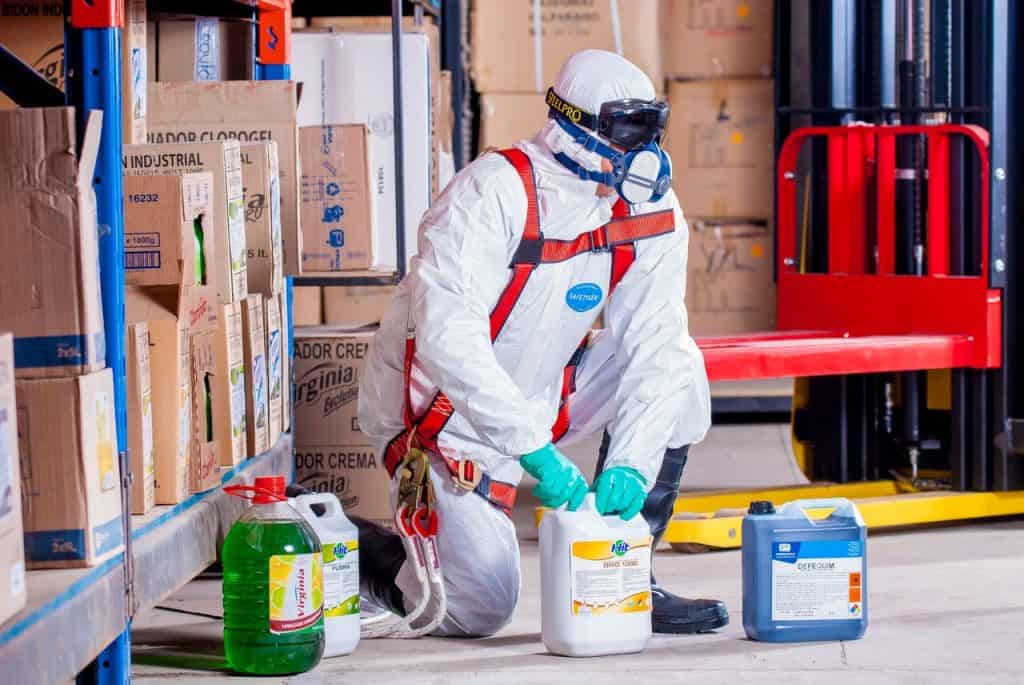
- This post has been written by an outside source – See Disclosure Policy